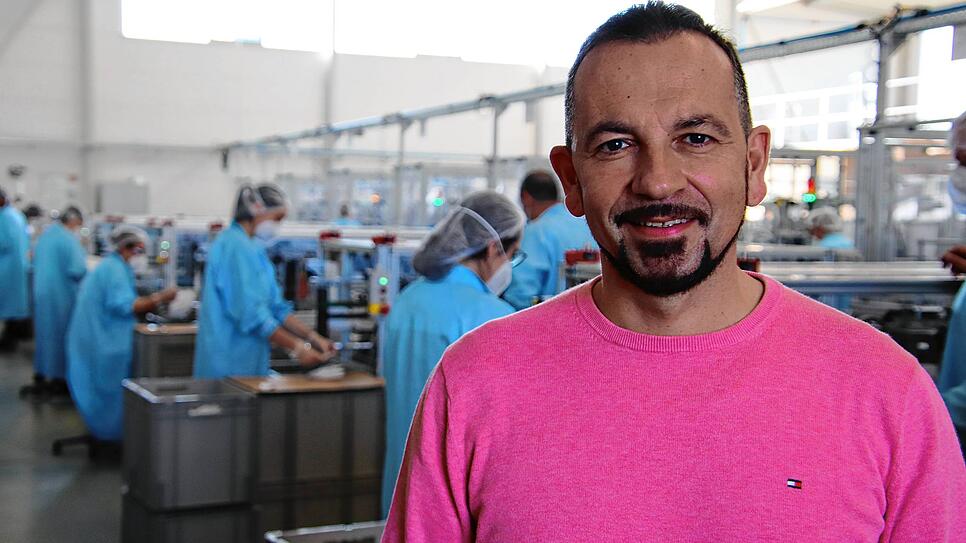
Als ein Winzling im Februar Deutschland, Europa und die ganze Welt in Schockstarre versetzt, hat Thomas Vosseler eine Idee. Der Unternehmer mit Dutt und kahl geschorenen Seiten will die Corona-Krise nutzen, Geschäfte machen und dabei etwas Gutes tun. Aber wie? Eigentlich vertreibt er zu dieser Zeit noch Gleitschirme. Medizinische Expertise hat er nicht. Als die Krankenhäuser vom Masken-Engpass erwischt werden, ist ihm das egal: FFP2-Masken müssen her. Und zwar dringend.
Vosseler schlägt sich Nächte um die Ohren, liest sich Wissen an, bewirbt sich bei der Ausschreibung der Bundesregierung – und ist erfolgreich. Er kauft zwei Masken-Produktionsmaschinen einer Schweizer Firma und legt los. Heute arbeiten bei Univent Medicals 120 Mitarbeiter. In diesem Jahr wird er 36 Millionen Masken herstellen – ein Viertel davon gehen an die Bundesregierung nach Berlin.
Vertrag mit der Bundesregierung bis Ende 2021
„Wir haben mit der Bundesregierung noch bis Ende 2021 einen Vertrag. Diese Sicherheit habe ich gebraucht. Sonst wäre das Risiko zu groß gewesen“, sagt Thomas Vosseler im Eingangsbereich seines Unternehmens.
Klar: Die Investitionen gehen in die Millionen. Was seine Masken von herkömmlichen FFP2-Masken unterscheidet, will Thomas Vosseler nicht im Detail verraten – Betriebsgeheimnis. Nur so viel: „Alles steht und fällt mit der Qualität der Rohstoffe und den Lieferanten.“
Aber auch ohne sein Prüfgerät wäre der Unternehmer aufgeschmissen. „Die Maschine kommt aus Karlsruhe. Sie kostet etwa 100.000 Euro. Wir hatten sie sogar noch vor dem TÜV„, beschreibt der Unternehmer sein Baby, wie er sie nennt.
Tatsächlich spielt die Maschine eine entscheidende Rolle im Univent-Zirkel. Denn nur mit dem „PMFT1000“ der Firma Palas lässt sich die Qualität der Rohstoffe für das Innenfutter einer FFP2-Maske überhaupt feststellen. Die Stoffbahnen kommen aus China in großen Rollen in Schwenningen an.
Es handelt sich um Meltblown. Aus dem englischen übersetzt, bedeutet der Begriff so viel wie geschmolzen und geblasen. „Das Material perfekt herzustellen, ist fast so schwer, wie einen perfekten Espresso zuzubereiten“, beschreibt Thomas Vosseler.
Warum? Es ist aufwendig. Und jedes Meltblown ist anders. Verkürzt gesagt, besteht Meltblown aus Polypropylen, einem Kunststoff aus der Textilindustrie. Polypropylen wird geschmolzen, bis es zäh ist. Dann werden dünne Fäden im Mikrometerbereich gesponnen. Im Anschluss werden diese Fäden zusammengeblasen. Bevor das Meltblown in die Produktion geht, werden aus jeder Rolle kleine Stücke herausgeschnitten und getestet.
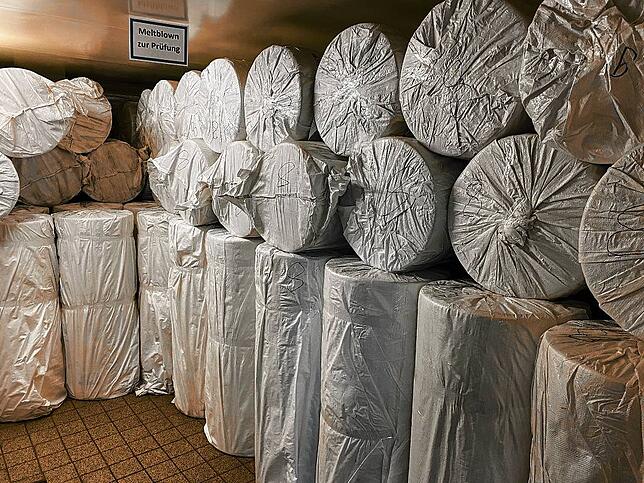
Thomas Vosselers Physiklaborant Nico Pitzschel nimmt das Material akribisch unter die Lupe.
Er spannt den Stoff in das Testgerät, schließt das Ventil und drückt den Start-Knopf. Vereinfacht gesagt, pustet die Maschine dann kleine Partikel Paraffin und Natriumchlorid durch den Stoff. Sie simulieren Aerosole. Diese verbreiten das Virus einer infizierten Person in der Luft. Die Maschine testet auch den Atemwiderstand – ein weiteres wichtiges Kriterium bei einer FFP2-Maske.
Sollte das Meltblown im Test durchfallen, wird die gesamte Rolle entsorgt. Seit Produktionsbeginn im Juli warf Thomas Vosseler Meltblown mit unzureichender Qualität im Gesamtwert von rund einer Million Euro in den Müll – unter anderem auch diese Rollen:
Bei positivem Testergebnis rollt der Stoff in die Produktionshalle.
Im ersten Schritt werden die unterschiedlichen Schichten übereinander gelegt und in Grundform gebracht. Dann wird der bewegliche Nasenbügel eingearbeitet.
Danach erhalten die FFP2-Masken ihre Ohrenhalterung. Dafür erhitzt die Maschine den Kunststoff kurz und drück ihn auf die Oberfläche der Maske. Ähnlich wie ein Wachssiegel auf dem Briefpapier.
Im Anschluss bringen Walzen die Masken in Form. Messer schneiden die Mund-Nasen-Bedeckung aus – alles voll automatisch. Der gesamte Vorgang dauert pro Maske etwa eine Minute. Hier noch einmal zusammengefasst.
Einen menschlichen Handgriff braucht die Maske aber noch. Denn nach der Herstellung prüft ein Mitarbeiter am Ende der Produktionskette in voller Schutzmontur, ob alles glatt ging.
Parallel läuft dieses Prozedere an acht verschiedenen Bahnen nebeneinander.
Bevor die Masken in eine Plastikhülle gesteckt und verschlossen werden, prüft Vosselers Laborteam noch einmal die Qualität. Zwei fertige Masken von jeder Rolle werden stichprobenartig unter die Lupe genommen. Erst wenn die Testmaschine auch hier grünes Licht gibt, werden sie in Kartons verpackt und ausgeliefert.
30 Stück landen in einer Box und werden an Unternehmen, Behörden und Krankenhäuser verkauft – ausschließlich in größeren Stückzahlen. „Wenn wir hier für jeden einzelnen Haushalt produzieren würden, wäre das viel zu chaotisch“, sagt Thomas Vosseler.