Wie entsteht das, was die Menschen in einem Auto schützt? Bei Constellium in Gottmadingen bot sich zwölf SÜDKURIER-Lesern kürzlich ein exklusiver Einblick in dieses Thema. Sie waren Teilnehmer an der Aktion ‚Der SÜDKURIER öffnet Türen‘, in diesem Fall zu den Gottmadinger Werkshallen von Constellium Automotive Structures – was man etwa als Autokomponenten übersetzen kann. In Gottmadingen produziert der Aluminium-Spezialist unter anderem den Teil eines Stoßfängers, der unter der sichtbaren Kunststoffschicht sitzt.
Wie Rainer Beyer, verantwortlich für das Europageschäft von Automotive Structures, erklärte, gehören zu den Leistungen aber auch Schweller für die Türen oder Dachspriegel – Querelemente, die das Dach eines Autos versteifen. Kunden: alle großen Namen der Automobilindustrie, so Beyer.
Vom Aluminium-Profil zum Stoßfänger
Was die 680 Mitarbeiter auf dem Werksgelände machen, konnte die Besuchergruppe dann hautnah erleben. Werksleiter Sébastien Riber, Bereichsleiter Benjamin Kohler und Patrick Böhler, der für die Produktentwicklung zuständig ist, nahmen die Gäste mit auf eine Tour durch die Hallen – vom ersten Aluminium-Profil zum fertigen Stoßfänger. In jedem vierten Auto in Europa seien Teile von Constellium enthalten, sagt Böhler.
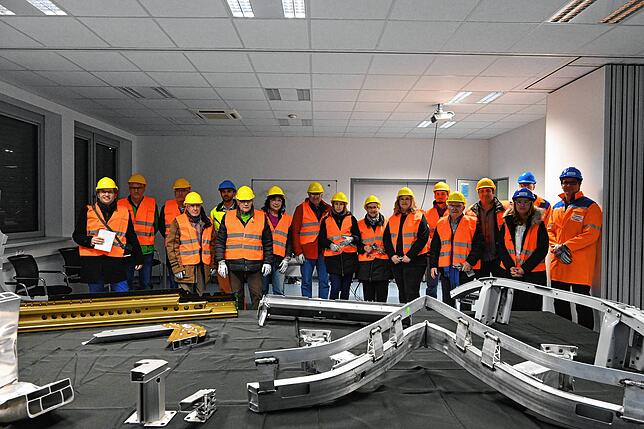
Das Aluminiumprofil für den Querträger im Stoßfänger komme schon in richtiger Länge aus dem Constellium-Presswerk in Singen, erklärte Riber. In einer Straße von Maschinen wird das Profil dann in Form gebracht. In einer Kombination aus Stanzen und Biegen werden zum Beispiel verschiedene Schraublöcher hergestellt und am Ende der Maschinenstraße stimmt auch die Krümmung. Zwischen den einzelnen Maschinen werden die Teile von einem Roboter weiterbewegt.
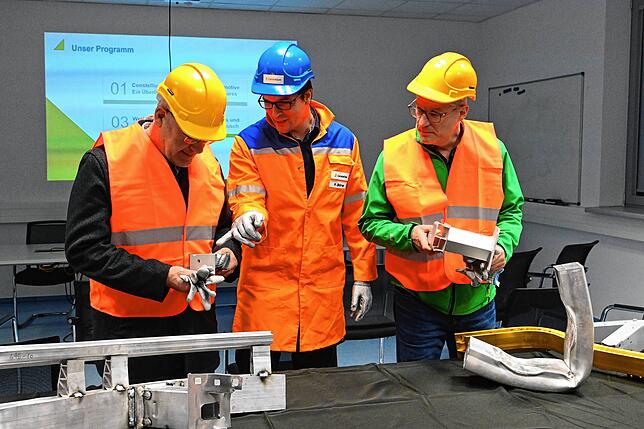
Die zweite Station auf dem Weg zum Stoßfänger ist der Absorber. Grob gesagt, sind das zwei senkrechte Elemente, mit denen der Unterbau des Stoßfängers an der Karosserie befestigt wird. Die Absorber sind so hergestellt, dass sie bei einem Aufprall maximal zusammengedrückt werden und so Crash-Energie aufnehmen – eben absorbieren. In diesem Fall müsse das Aluminiumprofil, das der Ausgangspunkt ist, erst noch zugeschnitten werden, erklärte Benjamin Kohler den Besuchern. Und dann seien viele kleine Werkzeuge nötig, die viele kleine Arbeitsschritte übernehmen.
Besucher der Führung dürfen selbst ran
Und der Absorber braucht noch ein kleines Bauteil, nämlich Distanzstücke. Sie halten das Bauteil stabil, wenn es an die Karosserie angeschraubt wird. An dieser Stelle durften die Teilnehmer der SÜDKURIER-Führung unter der Anleitung von Mitarbeiter Madeira Helder selbst aktiv werden und per Maschine die Distanzstücke einbauen – ein kleiner Praxisblock auf dem Weg durch die Werkshallen.
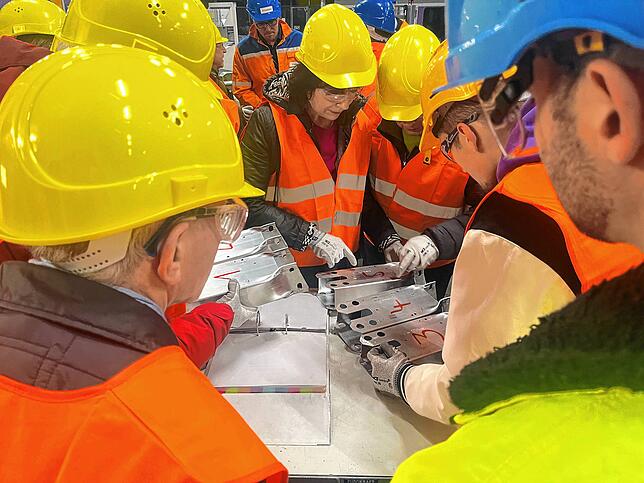
In großen Öfen werden die Bauteile dann je nach den gewünschten Eigenschaften erhitzt und dadurch gehärtet.
Nachhaltigkeit und Klimaschutz sind auch bei Automobilzulieferern ein Thema. Ob man an dieser Stelle von der Gasfeuerung weggehe, sei aber noch nicht klar, so Riber. Schließlich werden die Einzelteile des Stoßfänger-Unterbaus zusammengeschweißt – an einer automatischen Schweißstation. Die Stationen werden allerdings jeweils von einem Mitarbeiter mit den Einzelteilen bestückt.
Ihr Ende nahm die Tour im Messraum des Gottmadinger Werks, in dem Bauteile mit moderner Technik stichprobenartig auf Herz und Nieren überprüft werden – nur ein Teil der Qualitätskontrollen, die in dem Industriebetrieb permanent nebenbei laufen.
Und wie kam das bei den Besuchern an?
Sie löcherten die Constellium-Mitarbeiter mit zahlreichen Fragen. Und mit Sylvia Sorger war auch eine alte Bekannte der Belegschaft mit bei dem Besuch. Sorger hat selbst lange im Gottmadinger Constellium-Werk gearbeitet, vor neun Jahren habe sie dort aufgehört, erzählt sie. Zu aktiven Zeiten sei sie Anlagenbedienerin in verschiedenen Hallen gewesen. Und da man auch als ehemalige Mitarbeiterin nicht so einfach in die Werkshallen komme, habe sie es aus purer Neugier bei der SÜDKURIER-Aktion probiert – und Glück gehabt. „Es hat sich viel verändert“, sagt sie. Und: „Das gibt mir jetzt noch etwas.“
Hans-Georg Frank erzählt, dass er sich für alles interessiere, was mit Technik zu tun hat. Frühmorgens habe er in der digitalen Zeitung des SÜDKURIER von der Aktion gelesen, sich sofort für die Verlosung gemeldet – und dann auch über den Gewinn gefreut. Seine Erwartungen an den Besuch hätten sich voll erfüllt, sagt er. Ähnlich sah es Ulrich Keller. Die Technik unter den Hallendächern sei für ihn der Grund für die Teilnahme gewesen. Und was er dann sah, fand er sehr interessant.