Für viele bedeutet ein Studienabschluss zunächst einmal eine Hängepartie und ein Hangeln von Praktikumsplatz zu Praktikumsplatz. Dass es auch anders geht, zeigen David Lickert, Jan Hartmann, Andreas Baur und Noel Ernsting Luz. Sie sind alle zwischen 24 und 25 Jahren alt, haben ihre Studiengänge im Bereich Maschinenbau, Luft und Raumfahrt- sowie Elektrotechnik frisch abgeschlossen und bauen nun mit einer komplett selbst konstruierten Maschine in Windegg eine FFP2-Maskenproduktion auf.
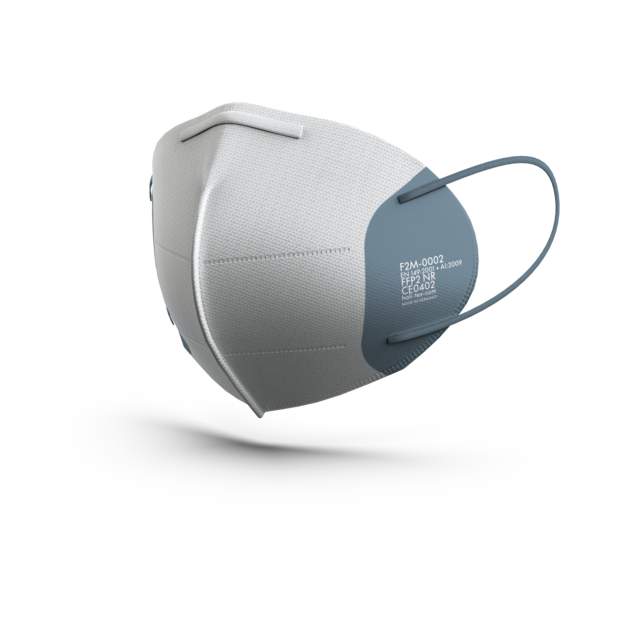
„Alles hat damit angefangen, dass wir uns darüber gewundert haben, dass es eigentlich nur einen Maschinentyp gibt, der zur Produktion von FFP2-Masken eingesetzt wird, und dieser aus China kommt“, erklärt David Lickert. Diese Maschinen müssten von drei bis vier Personen bedient werden, da viel Handarbeit anfalle, insbesondere, was die Verpackung der Masken angehe.
Pläne entstanden in der Küche
„Deshalb haben wir uns gedacht, das müssen wir im Manschinenbauerland Deutschland besser hin bekommen“, so Lickert. Und so haben sich die vier Freunde, die sich bereits aus der gemeinsamen Schulzeit kennen, in der Küche von Jan Hartmann zusammen gesetzt und angefangen eine eigene Maschine zur Maskenproduktion zu entwerfen. Das war im Frühjahr 2020. Rund ein halbes Jahr lang brüteten sie über der Konstruktion und den erforderlichen Details und machten sich mit den Anforderungen an die Produktion von FFP2 Masken vertraut.
Ein Problem sei das nicht gewesen. „Bei der Maskenproduktion geht es vor allem um die Umsetzung und Einhaltung bestimmter Normen und technischer Parameter. Das ist letztendlich nicht anders als in der Automobil- oder Luft- und Raumfahrtbranche. Darauf wurden wir schon im Studium getrimmt“, sagt Lickert und muss lachen.
Finanzierung war schwierig
Parallel zur Entwicklung der Maschine lief die Suche nach Geldgebern. „Das war gar nicht so einfach“, betont Jan Hartmann. So habe man sich etwa um Fördergelder bei der Kreditanstalt für Wiederaufbau (KfW) beworben, doch ohne Erfolg. „Fünf Wochen lang kamen immer wieder Rückfragen, am Ende wurde der Antrag abgelehnt. Vermutlich waren wir der Bank einfach zu jung.“
Mit Unterstützung der Sparkasse Reichenau klappte die Finanzierung am Ende doch noch. 1,3 Millionen brauchten die vier jungen Männer um dieses Projekt Wirklichkeit werden zu lassen. „Aber, dadurch, dass wir einen Kredit aufnehmen mussten, ist die Finanzierung sehr eng gestrickt. Wir wussten also, dass wir uns keine Fehler erlauben durften“, sagt Hartmann.
Mit offenen Armen in Windegg empfangen
Auch die Suche nach einer passenden Halle, in der die Maschine gebaut und eine erste Produktion eingerichtet werden konnte, stellte eine Herausforderung dar. „Wir wären gerne im Konstanzer Raum geblieben, aber das ist unbezahlbar“, sagt David Lickert. So sei man in Windegg gelandet. „Das hat alles sehr gut funktioniert, wir wurden hier mit offenen Armen empfangen“, erinnert sich Jan Hartmann. Auch die Zusammenarbeit mit der Stadt Stockach habe gut funktioniert.
Ende Dezember 2020 haben die vier jungen Männer dann die in Hartmanns Küche erarbeiteten Pläne zusammengepackt und sind in die Produktionshalle umgezogen, um die Maschine zu bauen. Dabei galt die Devise „Alles was wir selber machen können, machen wir auch selber“, betont Lickert. Parallel lief die Zertifizierung der Masken.
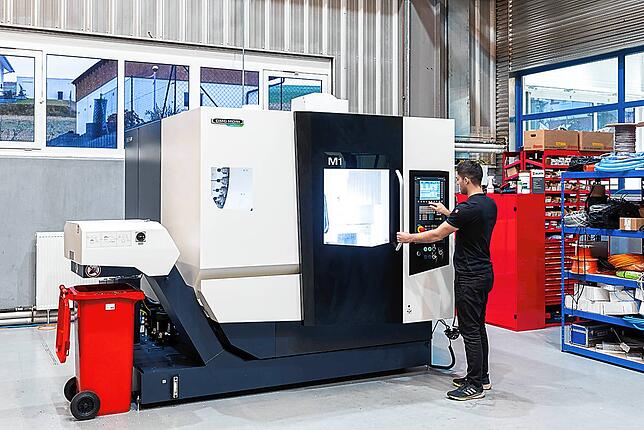
Dieser Prozess dauere ein bis zwei Monate. „Es war uns wichtig, die Masken bei einem seriösen Institut zertifizieren zu lassen. Am liebsten hier in Deutschland, allerdings laufen hier die Zertifizierungsprozesse noch deutlich langsamer ab. Deshalb wendeten wir uns an die Research Institutes of Sweden in Göteborg“, berichtet Hartmann.
Drei Anläufe habe man gebraucht, bis es am Ende mit der Zertifizierung geklappt habe. „Ein Anlauf zur Zertifizierung kostet dabei 30.000 Euro“, so Hartmann. Doch nun dürfen die Masken aus Windegger Produktion offiziell das CE-Siegel und die Schutzklasse FFP2 tragen. Laut Lickert und Hartmann filtern sie 94 Prozent aller Partikel aus der Atemluft.
Doch warum wurden aus den Maschinenbauern nun Maskenproduzenten? „Wenn man eine Maschine entwickelt, dann muss man auch gewährleisten können, dass sie lange Zeit einwandfrei funktioniert“, erklärt David Lickert. Deshalb steige man zunächst selbst in die Produktion ein, quasi um die Maschine dem Langzeittest zu unterziehen.
Alles funktioniert automatisch
Das Besondere an der Maschine sei, dass sie von einer einzigen Person bedient werden könne. Vom Rohstoff bis zur fertigen Maske sei kein einziger Handgriff mehr notwendig. Somit können höchste hygienische Standards bei der Maskenproduktion eingehalten werden, machen Lickert und Hartmann deutlich.
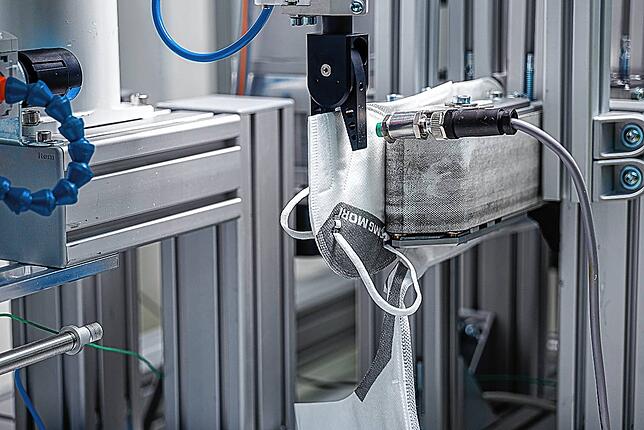
Vor kurzem startete nun die Produktion der Masken unter dem Namen Hali-Tex, verkauft werden sie über den eigenen Online-Shop. Doch kommen die vier jungen Männer mit ihrer Entwicklung inzwischen nicht zu spät? „Nein“, sagen sie. Sie wollen auf Qualität setzen, und gehen davon aus, dass es dafür auch einen Markt gibt. „Wir beziehen unsere Rohstoffe aus deutscher Produktion. Aufgrund der hohen Qualität sind unsere Masken besonders angenehm zu tragen und ermöglichen leichteres Atmen als viele Masken aus China.“ Zudem könnten die Masken aus Windegg mit einer speziellen lebensmittelechten Serviettentinte bedruckt werden, etwa mit Firmenlogos und seien damit personalisierbar.
Einige Kunden habe man bereits an Land gezogen. „Das war aber gar nicht so einfach, oft wurde sofort aufgelegt, wenn wir versucht haben, Angebote für FFP2-Masken abzugeben. Unsere potentiellen Kunden bekommen teilweise bis zu 30 E-Mails mit Angeboten für FFP2-Masken pro Tag“, berichtet Hartmann. Da sei es schwierig überhaupt schildern zu können, was das Besondere an dem Produkt sei. Allerdings gebe es abgesehen vom Masken-Geschäft auch schon Ideen für zukünftige Projekte im Stoff-Bereich, die sich mit Weiterentwicklungen der Maschine umsetzen lassen, sagt Hartmann.