Firmen, die in der Corona-Krise mit guten Nachrichten aufwarten können, sind selten geworden. Doch es gibt sie. In Illmensee steht im Neubaugebiet eine riesige Halle. Darin werden wichtige Teile für medizinische Anlagen produziert, die zum Beispiel in Krankenhäusern eingesetzt werden. Medizinische Geräte für Untersuchungen, die unter anderem dazu beitragen, dass Corona schnell erkannt und zielgenau behandelt werden kann, und deshalb höchsten Anforderungen genügen müssen.
Mitten in der Pandemie sind diese Teile sehr gefragt: „Durch diese speziellen Anfertigungen ist es uns gelungen, auch in der Corona-Krise unter dem Strich ein Umsatzplus zu verzeichnen“, sagt Peter Müller. Er ist Chef der Firma Müller Maschinenbau, die mit derzeit 34 Mitarbeitern schwerpunktmäßig komplexe Maschinenbauteile im Einzelteilbereich fertigt.
Erfolgsgeschichte beginnt in Pfullendorfer Garage
Die Erfolgsgeschichte des Unternehmens beginnt in einer Garage in Pfullendorf. 2006 stellte Peter Müller dort eine Drehmaschine auf und gründete seine erste Firma im Nebenerwerb. Fertigungsschwerpunkt waren damals ganz klassische Dreh- und Frästeile. Zuvor hatte er nach der Ausbildung zum Werkzeugmechaniker seinen Meister gemacht und war einige Jahre als Produktionsleiter in einer Firma angestellt. „Mit 24 Jahren habe ich mich selbstständig gemacht“, schildert Müller die Anfänge seiner von Unternehmergeist und innovativen Erfindungen geprägten Karriere.
Ein weiterer Firmensitz von Müller Maschinenbau war zuerst eine angemietete Halle in Ochsenbach, ab 2008 dann in Illmensee, bevor Peter Müller mit seinem Team im Jahr 2012 endgültig in das Gewerbegebiet in Illmensee umsiedelte. „1000 Quadratmeter war unsere erste eigene Halle groß. Im Jahr 2018 haben wir eine weitere, gleichgroße Halle gebaut“, schildert der Firmenchef die ständige Expansion des Unternehmens.
Vier Auszubildende lernen derzeit im Illmenseer Betrieb
Schon bald habe er angefangen, zu konstruieren, zu entwickeln und schließlich auch Sondermaschinen zu bauen, erzählt er. Mit der Zeit habe sich das Geschäft immer weiter in Richtung Schwermaschinenbau gewandelt, also hin zur Bearbeitung von Großteilen im Dreh- und Fräsbereich. Die Firma etablierte sich auch als Ausbildungsbetrieb. Derzeit lernen vier Azubis dort den Beruf des Zerspanungsmechanikers.
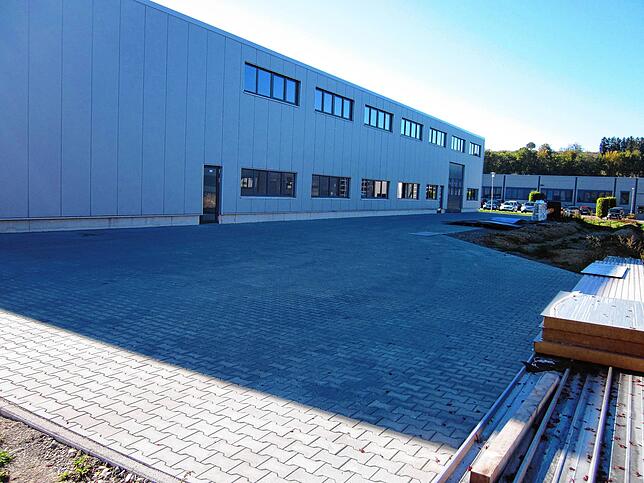
Das Leistungsspektrum des Unternehmens reicht von Konstruktion, Entwicklung, CNC, Drehen und Fräsen bis zu Schweißkonstruktionen und vieles mehr. Im hochmodernen Maschinenpark bearbeiten die Mitarbeiter Werkstücke mit bis zu zwei Metern Durchmesser. Unter Einhaltung der Corona-Hygiene- und Sicherheitsauflagen gehe das Geschäft derzeit auf gewohnte Art weiter, so Peter Müller „Wir suchen ständig nach neuen Mitarbeitern“, sagt der Unternehmer. Das sei schon 2008 so gewesen und das bleibe auch 2020 so. Das Unternehmen werde jährlich größer. „In der gesamten Zeit der Corona-Krise gibt es bei uns bisher keine Kurzarbeit und darauf bin ich besonders stolz“, betont Peter Müller.
Teile werden auch für Wind- und Wasserkraftanlagen benötigt
Benötigt werden die in Illmensee gefertigten Teile nicht nur für die Medizin, sondern zum Beispiel auch für Wasser- und Windkraftanlagen oder im Bereich der Bahntechnik. Die Kunden der Firma sind überall in Deutschland angesiedelt. „Darunter sind auch einige Global-Player, also Unternehmen, die in die ganz Welt exportieren“, verrät Peter Müller. Mit dem Bau von Sonderteilen hat sich Müller Maschinenbau regional in einer Nische etabliert. „Im Landkreis Sigmaringen gibt es viele Betriebe, die kleine Drehteile herstellen, aber nur ganz wenige, die Teile in dieser Dimension fertigen, wie wir das tun“, erläutert der Firmenchef. Es gebe kaum Betriebe, die so relativ klein seien und dabei gleichzeitig so große und moderne Maschinen verwenden, sagt Müller. Das sei ein großes Plus für die Firma.
Zehn Millionen Euro in vergangenen Jahren investiert
Nicht nur viel Arbeit und Ideen hat Peter Müller in die Firma gesteckt, sondern auch jede Menge Geld. Er überschlägt, dass er in den vergangenen Jahren inklusive der beiden Hallen rund zehn Millionen Euro investiert hat. Sein Erfindergeist ist noch nicht ausgeschöpft. Jetzt hat er sich den so genannten „Kompaktvereinzeler“ patentieren lassen. Damit will er unter andere die Fertigungsstraßen der großen Konzerne verkürzen. „Ich war bei einer Werksführung eines Automobilherstellers, da ist mir die Idee zu dieser Erfindung gekommen“, schildert Peter Müller. Der Kompaktvereinzeler soll mit einer sehr komplexen Technik bis zu 100 Nieten pro Minuten zur Verfügung stellen.
Drei Jahre Arbeit in neues Projekt gesteckt
„Überall, wo man etwas automatisiert montiert, soll das Gerät zum Einsatz kommen. Es sortiert die Nieten und Schrauben, führt diese der Montagestelle zu und baut sie ein“, erläutert der Unternehmer. So werde der Prozess des Zusammenbauens optimiert. „Wir haben zuerst Simulationen am Computer vorgenommen. Nach vielen Optimierungsphasen und drei Jahren Arbeit ist das Produkt jetzt fertig“, sagt er.
Mit neuem Gerät den Markt erobern
Das Gerät hat sich Peter Müller patentieren lassen. Bis Patentzuteilung und Serienreife erreicht worden waren, galt es, einige Hürden zu nehmen. Der Kompaktvereinzeler könne auch bei der Montage von Elektrogeräten eingesetzt werden – generell in allen Bereichen, in denen Produkte zusammengesetzt werden. „Jetzt geht es darum, den Markt zu erobern. Das ist eines der großen Projekte, die bei uns in den kommenden Jahren anstehen“, blickt Peter Müller hoffnungsfroh in die Zukunft.