Rund sechs Kilometer Fahrtweg und deutlich weniger Luftlinie trennen die Zeppelin Aviation & Industrial Service GmbH – eine lokale Ausgründung, bis Ende 2019 handelte es sich um einen Geschäftsbereich von Zeppelin Systems – und den Zeppelinhangar, in dem der neue Zeppelin NT zusammengebaut wird. Das letzte Mal am Bau von Luftschiffen beteiligt war das Team hier bei einem Auftrag aus den USA – die Luftschiffe, die dorthin geliefert worden seien, waren allerdings etwas anders aufgebaut: komplett starr und verstärkter als die deutsche Variante. Das erläutert Dafne Joel von der Geschäftsleitung, die persönlich durchs Werk führt.
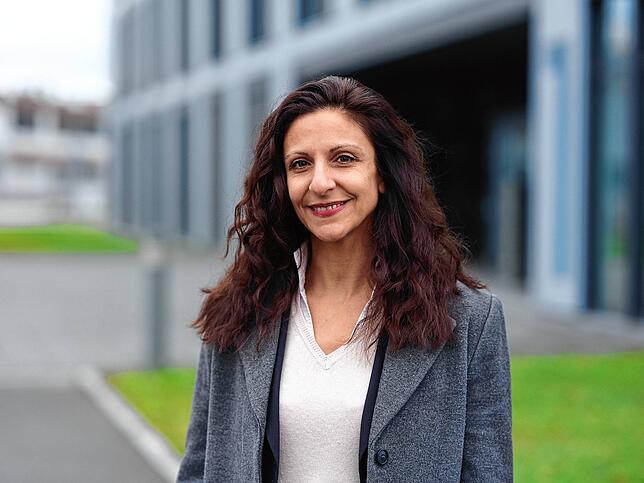
Neuer Zeppelin NT baugleich mit Vorgängern
Der Zeppelin NT, der nun gebaut werde, sei hingegen baugleich mit den Luftschiffen von vor zehn Jahren, erläutert Joel weiter, die seit 2010 in der Luftfahrt tätig ist. Das habe allein schon genehmigungsrechtliche Gründe. In der Luftfahrt – das betreffe auch Luftschiffe – müsse alles genau erlaubt und abgenommen sein, daher würden Baupläne eher selten geändert.
Bei dem Luftschiff aus Friedrichshafen, das mit weniger starrer Struktur auskommt als die US-Variante, kommt es dabei vor allem aufs Gewicht an. Die 39 Längsträger, die später zusammen mit einem Querträger, dem sogenannten Knochen, sozusagen das Skelett des Zeppelins bilden, werden hier vor Ort gefertigt. Das heißt, eigentlich werden nur 24 neu zusammengebaut. „Die übrigen 15 lagern schon im Hangar, die sind bei einem Umbau gegen eine andere Trägerart ausgetauscht worden“, so Joel.
In den Alubauteilen steckt ganz schön viel Handarbeit – auch die Maschinen werden manuell bedient und nicht etwa vorprogrammiert. Es wird geschweißt, gefräst, geschliffen und auch der Zusammenbau von Leiter- über Dreieckstadium erfolgt bis hin zu letzten Details meist händisch.
Wieso das heutzutage nicht automatisiert abläuft? Joel erklärt: „Die Längsträger haben eine unterschiedliche Krümmung, je nachdem, wo sie später platziert sind. So sind nur die wenigsten von ihnen komplett identisch.“ Zwischen drei und acht Meter sind die Träger lang, von denen später jeweils 13 zusammengesteckt werden. Für einen automatisierten Prozess brauche es hingegen baugleiche Teile in nennenswerter Anzahl. Sonst bedeute die Programmierung der Maschinen mehr Aufwand als die Fertigung der Teile selbst.
2015 wurde zuletzt ein ganzes Luftschiff gebaut
„Das letzte ganze Luftschiff wurde 2015 in Friedrichshafen gebaut, das waren die drei Goodyear-Schiffe, da haben wir drei Strukturen dazu beigetragen“, erzählt Dafne Joel. Mal werde ein Luftschiff gefertigt, dann wieder bis zu einigen Jahre gar keins. „In der Zwischenzeit fertigen wir dann nur ein paar Ersatzteile für den Zeppelin“, schildert sie, der Luftschiffbau sei somit nur ein kleiner Teil ihres Geschäfts. Das mache es schwierig, Experten für exakt diese Arbeiten zu gewinnen und zu halten.
Schweißexperte Johannes Hirscher arbeitet derzeit daher immer wieder fast allein an den Trägerstrukturen aus Alu. Er bringt jahrelange Erfahrungen mit dem Zeppelin mit. Die Schritte erfordern Übung; es kommt auf jeden Millimeter und jedes noch so kleine Zusatzgewicht an. Bei weniger als 13 Kilogramm Gesamtgewicht eines Längsträgers schlagen sich bereits die kleinsten Abweichungen nieder.
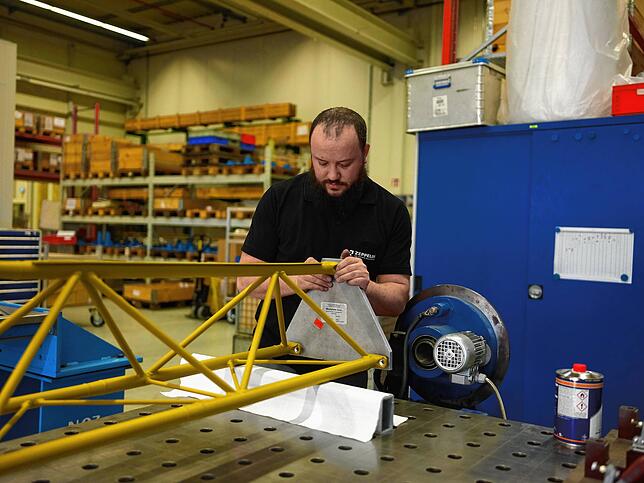
Prüfender Blick
Bei der Abnahme der Teile hat er allerdings Hilfe: Gemeinsam mit seinem Kollegen Kevin Heilig, ebenfalls ein Schweiß-Experte, prüft er die ersten fünf der Träger, bevor sie ausgeliefert werden. Dabei spielt nicht nur das exakte Gewicht eine Rolle, sondern auch etwa, dass die feinen Aluschienen, die oben auf den Trägern angebracht sind, keine scharfen Kanten haben. Auf ihnen wird später die Zeppelinhülle aufliegen. Obendrein prüft er den Sitz der Anschlussteile an den Enden der Träger, mit denen sie später zusammengesteckt werden. „Leichtgängig muss sie sein“, erklärt er, es gebe hier nur einen sehr kleinen Spielraum für Abweichungen.
Auch die Spezialrohre, aus denen die Träger dann zusammengesetzt werden, werden extra hier vor Ort gefräst, schildert Joel. Selbst der Anhänger, auf dem die fertigen Träger schließlich von Friedrichshafen nach Friedrichshafen geliefert werden, sei eine Sonderanfertigung. Die Alukonstruktionen sollen sicher an ihr Ziel kommen.
Im Hangar gilt die Aufmerksamkeit den anderen Zeppelinen
Am 21. Dezember wurden die ersten Längsträger geliefert, im neuen Jahr sollen die übrigen folgen. Im Zeppelinhangar passiert derzeit nichts am neuen Luftschiff. Dort findet die Jahresinspektion der beiden anderen Zeppeline statt. Auf die Lieferung der Gondel, die dann vor Ort mit Elektronik – vor allem vielen Hundert Meter Kabeln – bestückt werden soll, wird außerdem gewartet. Derzeit gibt es keinen Liefertermin für diese, erklärt Marketingreferent Aaron Willers von Zeppelin NT. Ursprünglich einmal war die Gondel für Ende August angekündigt gewesen.