Die Veranstaltungsreihe „SÜDKURIER öffnet Türen“ führte rund 20 ausgeloste Abonnentinnen und Abonnenten – es hatte knapp 140 Bewerbungen gegeben – in das Meßkircher Unternehmen Alber Treppensysteme. Dort konnten sie erfahren, wie ausgehend von einer 3D-Konstruktion am Computer aus massiven Holzplatten eine Treppe mit Stufen, Wangen und Handlauf entsteht.
Geschäftsführer Jürgen Alber musste von Manfred Dieterle-Jöchle, Leiter der SÜDKURIER-Lokalredaktion Meßkirch, nicht lange überredet werden, die Türen seines Betriebs zu öffnen. Alber gefiel die Idee, interessierten Gästen einen Blick hinter die Kulissen zu ermöglichen. „Ich finde das Format gut.“ Für ihn sind Treppen nicht nur funktional, um nach oben oder unten zu gelangen. „Treppen sind Möbelstücke“, so Alber, der nach seinem Holztechnikstudium 2004 in den elterlichen Holzbau-Betrieb eingestiegen war und die Treppenbausparte übernahm. Heute beschäftigt Alber Treppensysteme 65 Mitarbeiterinnen und Mitarbeiter.
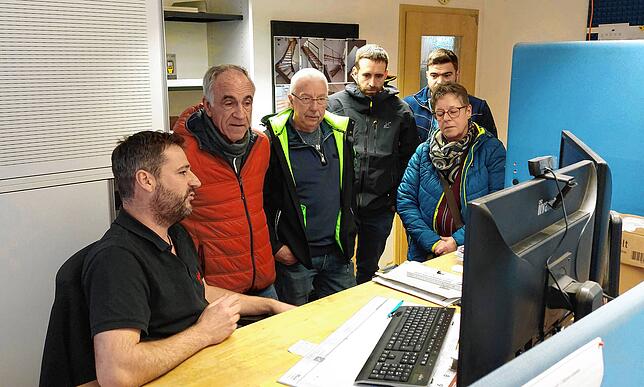
Extra den Feierabend verschoben
Damit die Besuchergruppe auch laufende Maschinen zu sehen bekam, hatten die Mitarbeiter ihren Feierabend extra nach hinten verschoben. „Ich selber komme aus dem Metallbereich und interessiere mich für die Technik bei Alber“, erklärte Christian Greiter aus Rohrdorf, warum er an der SÜDKURIER-Verlosung teilgenommen hat. Brigitte Schmon aus Altheim, die ihren Mann Karl begleitete, zeigte sich beeindruckt angesichts der automatisierten Abläufe: „Als Laie sieht man nur das tolle Ergebnis, aber weiß gar nicht, wie eine Treppe produziert wird.“
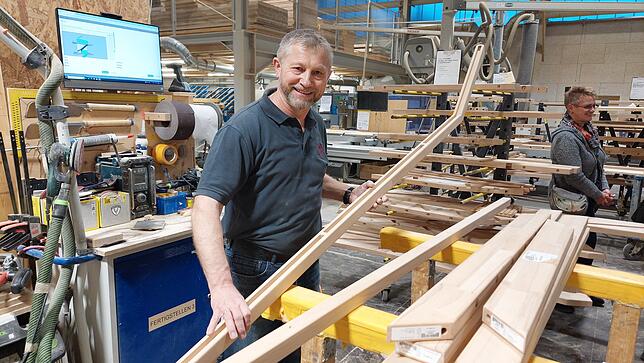
Zimmerei wird 1986 gegründet
Bevor der Rundgang durch die Produktionsstätte begann, umriss Jürgen Alber kurz die Geschichte des Familienbetriebs. Sein Vater, Franz Alber, hatte sich 1986 mit einer Zimmerei in der Meßkircher Conradin-Kreutzer-Straße selbständig gemacht. Der Treppenbau funktionierte damals noch ganz händisch. Aufrisse, sprich die Zeichnungen im Maßstab 1:1, wurden direkt auf am Boden liegende Spanplatten gezeichnet. „Der erste Computer 1990 war ein Quantensprung“, erinnert sich Alber. Die erste CNC-Maschine kam 1994 zum Einsatz. Weil es in der Stadtmitte zu eng wurde, entschloss sich Familie Alber 2000 für einen Neubau im Weidenäcker. „Wir hatten am neuen Standort drei Mal so viel Fläche wie in der Stadtmitte und sind weiter gewachsen.“ 2013 kam noch ein markantes Ausstellungsgebäude an der Bundesstraße 311 hinzu.
Staunen über Vollautomatisierung
Jürgen Alber und der zweite Geschäftsführer, Daniel Haack, führten die Gruppe durch die Konstruktionsbüros und weiter in die moderne, nahezu voll automatisierte Produktionsanlage. Dort konnten die Besucher vom Zuschnitt bis zum Lackieren die Fertigungsschritte nachvollziehen. Besonders beeindruckt waren die Gäste von den großen Präzisionsmaschinen. „Das ist faszinierend“, meinte Wolfgang Kuhn aus Pfullendorf. „Im Haus meines Sohnes wurde gerade eine Treppe eingebaut und ich habe gestaunt, wie genau das alles auf der Baustelle passte.“
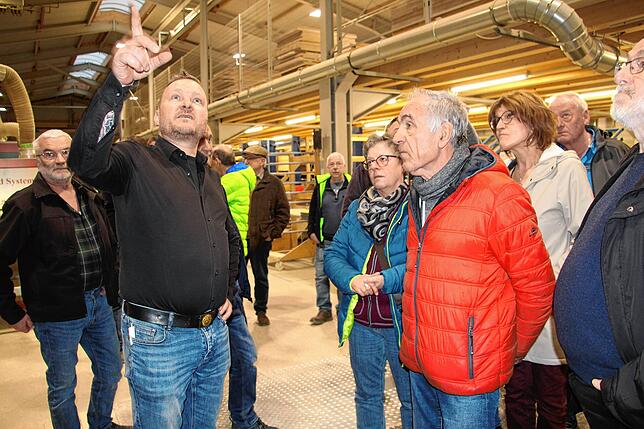
Abfallholz zum Heizen
Damit die Platten auf dem Frästisch nicht wackeln – denn schließlich geht es um Millimeter – werden sie von unten mittels Vakuumpumpen an Ort und Stelle gehalten. Über große Schläuche gelangen abgesaugte Späne in einen Turm. Sie wandern, wie das Abfallholz, zur Verbrennung in eine Hackschnitzelanlage. Die Wärme heizt die Produktionshalle. Abfallholz soll natürlich so wenig wie möglich entstehen. „Das ist ein wertvoller Rohstoff, mit dem wir verantwortungsvoll umgehen“, stellte Alber fest. Also kommt es auf eine optimale Programmierung an, um so viele Bauteile wie möglich aus einer Platte zu erhalten. „Aus einer Platte fräsen wir Bauteile für verschiedene Aufträge. Damit die Teile am Ende richtig zusammengeführt werden, wird jedes automatisch mit einem Barcode etikettiert.“
Die verschiedenen Treppentypen und Absturzsicherungen konnten sich die SÜDKURIER-Leser am Ende der Führung noch im großen Ausstellungsgebäude anschauen, wo sie von Denise Alber schon mit Getränken und Butterbrezeln erwartet wurden.